What is 5S
Many companies have implemented 5S in offices, factories and even hospitals around the world. The 5S methodology is a great tool to help you start your journey on improving your work area.
5S is a method used to organize and standardize different work areas or stations to maximize efficiency and quality. The 5S method uses the different “S’s” to have a home for every part and tool in the work area. There are special markings for each item that are clearly labeled and identified so each team member knows where each item can be stored.
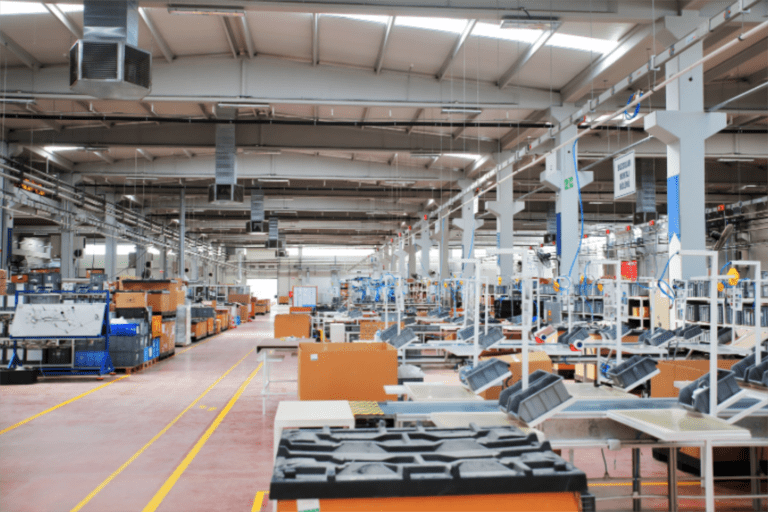
There are many other benefits to 5S that we will review in the next few chapters. The origin of the 5S process was developed in Japan by Toyota many years ago to helping them to be one of the top car manufacturers in the world.
Many companies around the world now use this process to improve anything from Factory work stations to office cubicles. 5S is a great way to organize any area and to help train all team members how to reduce waste and improve productivity.
What are the Benefits of 5S
There are many benefits to using 5S in your company but we will focus on the few listed below.
1. Safer Work Environment
Imagine walking into an area where there were air lines on the floor and a general mess in the area. These items could cause a major injury and lead to some loss of time for an employee that got hurt in the area because the area was not organized and a standard was not set in place for the work area.
If the air line was put away or overhead, then there would be no trip hazard and reduces the risk of anyone getting injured. If a work area is organized and clean, this will reduce the potential of anyone getting hurt.
2. Higher productivity
When I tell engineers that implementing 5S will improve productivity, some are surprised. If a person working in an area knows that a tool will always be in the exact same place each time they need to use it, this will help them reduce time getting a tool. If this person reaches for 10 tools to complete this operation, they have made the process more efficient and the operator is more productive.
3. Better quality
A new 5S area will have a dedicated process and procedure on how to complete tasks in their workstation. When the products are all built the same and follow the process that the manufacturing engineer has set in place, the product will be made the exact same way. This will allow the inspectors or the team member in the next cell to review the work of the previous cell.
When the product or service that your team offers to a customer is built in a consistent manner following the work procedures, you will see your warranty numbers reduce. With the reduced number of defects on the line, you will see fewer warranty claims coming from your customers
This consistency in the process will make it easier for all assemblers to build in the correct sequence, therefore reducing overall defects due to repetitive work being followed
4. Reduce cost
The overall cost to run the factory will reduce because you now have fewer parts being lost, the work is completed faster and you have a better quality product leaving your facility
What are the 5S's
Sort – Clear out rarely used items (red tag)
The first exercise in starting a 5S is to clear out all items that are not required in the area and a rarely used, this is the Red Tag Process. The Red Tag process starts with a team of people working with the operator in the area to remove any unused items in that work cell. All the unwanted items will be identified with a red tag and moved out of the work area.
This removes any clutter and tools that are not used so you can make room for the racks and organizational system you put in place in the next steps.
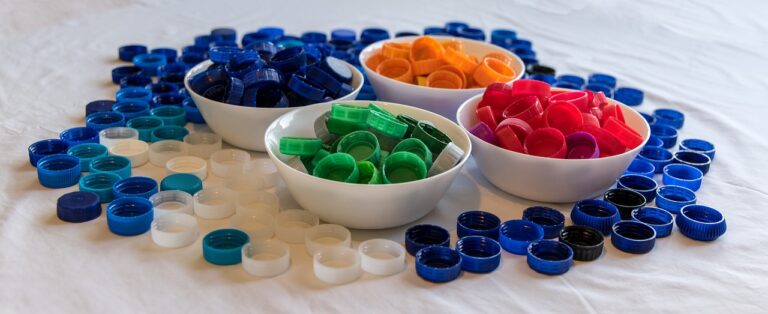
Straighten – Organize and label
After all of the Red Tag items have been removed from the area, it is time to organize the different items that are in the area. Each item that you have in the area needs a plan on how you will organize items and how you will label them.
Place all the tools on a standard workbench making it easier to find when the worker in the area is looking for them. Try using a shadow board, below is a similar shadow board to what you would see in a 5S factory.
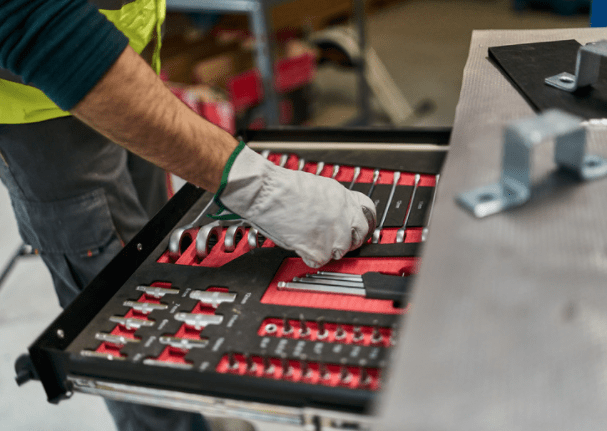
Place all parts on a rack that can be easily accessible for the workers in the area and the materials team that is putting parts away in the rack. Once the parts are organized in the racks, now you can work on making labels for each part number to place on the racks. This is the home location for that part and can be always found in this spot.
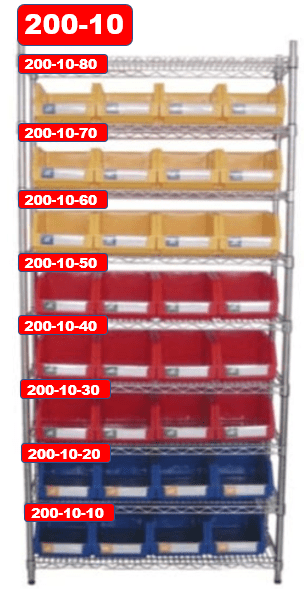
Shine – Clean it
It is quite common for companies to give all work teams 5 minutes at the end of the day to clean there are and place all tools and fixtures back in the home locations. Each work center that is practicing 5 needs to have all cleaning supplies in their area for team members to clean at the end of the shift.
When the cleaning process is done properly, you will visually be able to see what is out of place and what items need to be cleaned up or needs to be put away.
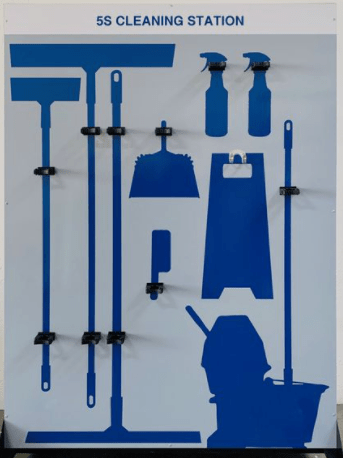
Standardize – Rules to keep first 3S’s
Now that you have completed the Sort, Straighten and Shine, in one area, you now need to create a standard for your company. Remember the pictures you took of the tool boards and the parts racks when you were organizing the area, these pictures will now be used to standardize how you would like this work center to look like every time you inspect it. The standard sheet will be posted in the area for all auditors and supervisors to see.
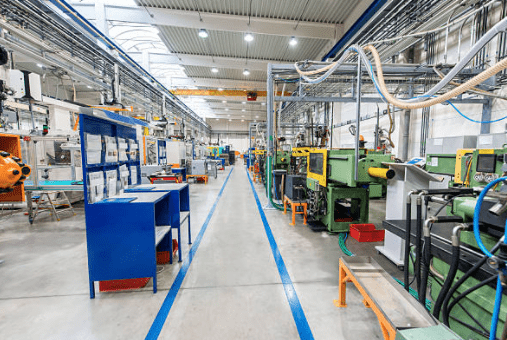
A 5S communication board is used to convey messages to the team working in the cell and is also used to show the team from month to month if they are improving or need help to achieve their 5S goals.
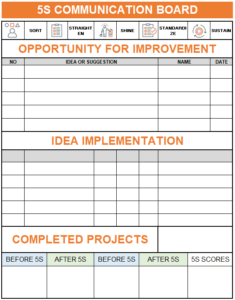
Sustain – Audit Areas To Stay Discipline
Maintaining the fifth S, Sustain is incredibly challenging for any organization. Regular audits are necessary to ensure that the work area remains as clean and organized as the team left it. These audits will help verify that the staff is keeping the 5S area in good condition, just like the showcase area.
The audits are to be completed by supervisors or managers who have been trained in the 5S standard that you and your team create during the standardization phase.
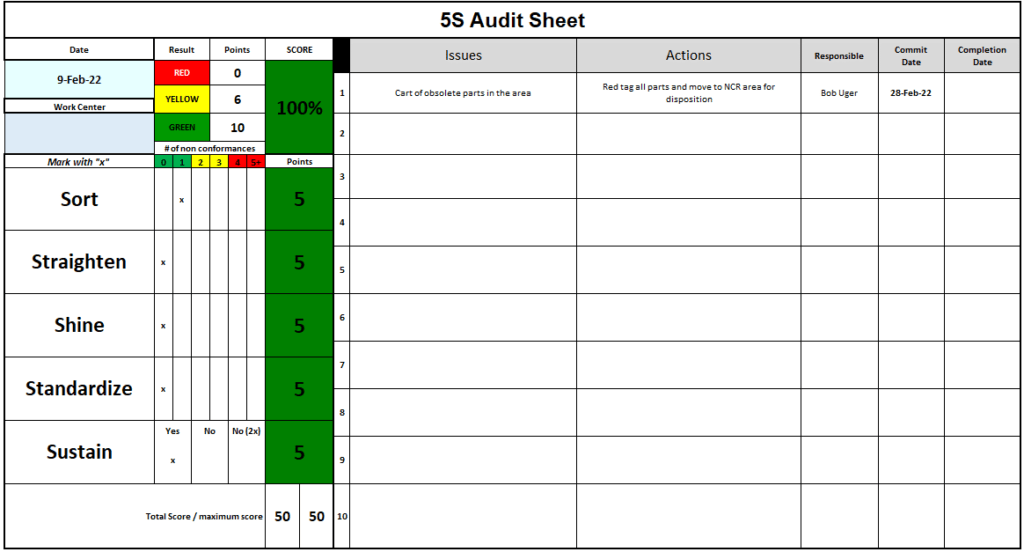
5S is not Lean Manufacturing, it is only a tool in Lean
Some managers mistakenly believe that implementing 5S in their factory automatically means that they have achieved a Lean Manufacturing status. However, this is not the case. While 5S is a helpful tool in achieving a Lean Manufacturing factory, it is not sufficient on its own. To become a Lean Manufacturing company, you will need to implement several other Lean tools in addition to 5S. Although 5S does help in removing waste (Muda) from a work area, you will need to focus on the other pillars of lean to achieve a truly Lean Manufacturing company.
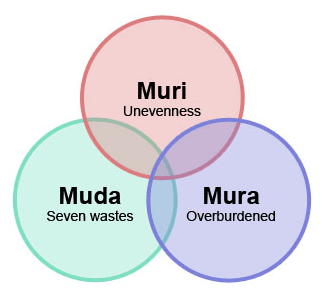
Muda – Waste
Mura – Unevenness
Muri – Over Burden
If you would like to learn more on Lean Manufacturing, click on the link below to see our article that explains what you need to accomplish Lean in your business.
LINK
TO LEAN MANUFACTURING BLOG
If you would like a free 5S audit template, click the link below.
LINK TO 5S SUPPORT DOCUMENTS