Shine - The Third 5S
Sorting and Straightening your work area was a good introduction for the team in the work area on how 5S works. When managers, supervisors, and staff collaborate to create a 5S showcase area, it boosts morale and fosters teamwork among the staff working in the process. This showcase area can serve as a model for other 5S areas in your process.
Shine is an important step in setting the standard of what the work area needs to look like and the cleanliness level that the staff in the work area needs to maintain daily. The work area may have seemed very messy and dirty after you remove unwanted items from drawers and shelves, it is now time to clean everything in the work area.
As implied the third 5S Shine, means that everything in the work area needs to be cleaned. Yes, everything. You and your team will need to clean each shelf, under racks, floors and drawers. This is done to set a cleanliness standard for all work areas and make it easier to clean on a daily basis. By cleaning everything and setting a standard for your showcase area, you have shown every staff member who works in the process what your definition of clean is.
The next part of this article will give you a bit of guidance on how to Shine your work area. I know that most of you are saying, of course, I know how to clean, however, you must teach others the standard you would like to see in a showcase 5S area.
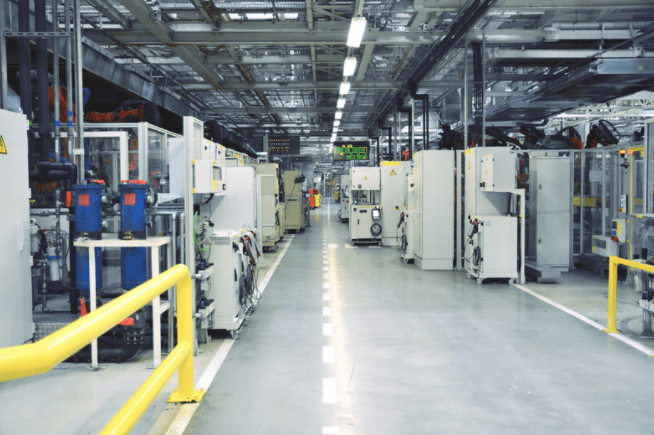
Step 1 - Clean The Area
After your 5S Sort, you have probably uncovered a lot of dust and dirt in corners and on shelves in the work area. When I say we are cleaning the area, I mean we are doing a deep cleaning of the work area. Time to break out the wet rags and mops so everyone can mop the floor and clean any dirt or grease. Have buckets with warm water and rags ready so you can clean all the racks and tools so there is no dust or grease on them. When you clean the racks, make sure that you reach under the racks and lift the parts bins to clean under these bins.
It is important to clean the area because it makes all the following steps much easier to implement when the work areas are clean.
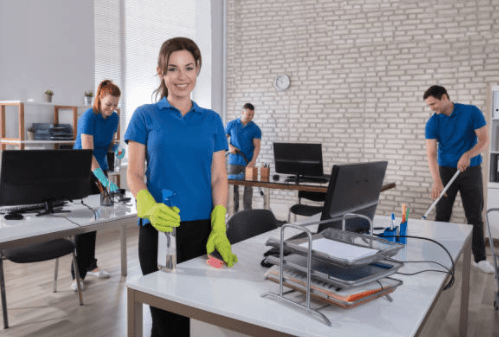
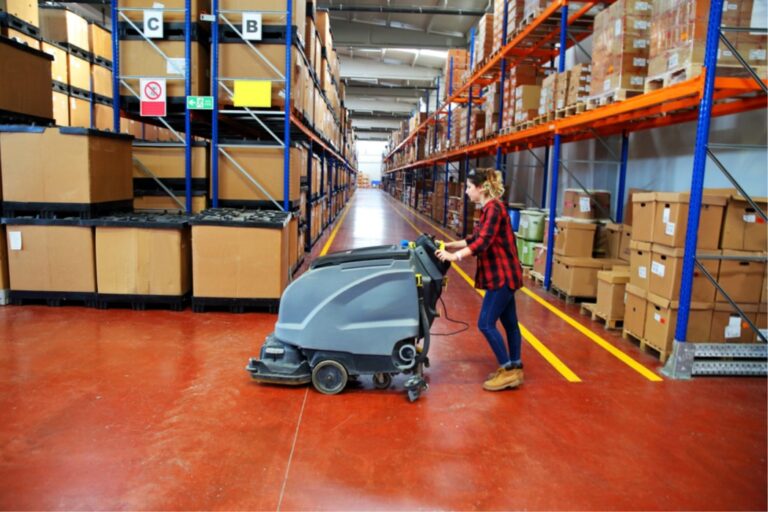
Step 2 - Set Cleaning Goals
All 5S factories have goals of what needs to be cleaned each day in all work areas. Depending on how big the work areas are, you will need to break the cleaning routine into different days. Each day will have a different deep clean item as well as the regular daily cleaning.
I have found that placing a 5S cleaning checksheet in each work area has produced excellent results. This helps the teams working in these areas to know which items need to be cleaned each day. Below is an example of a typical 5S cleaning checksheet that you can use as is or modify the template that is available for download.
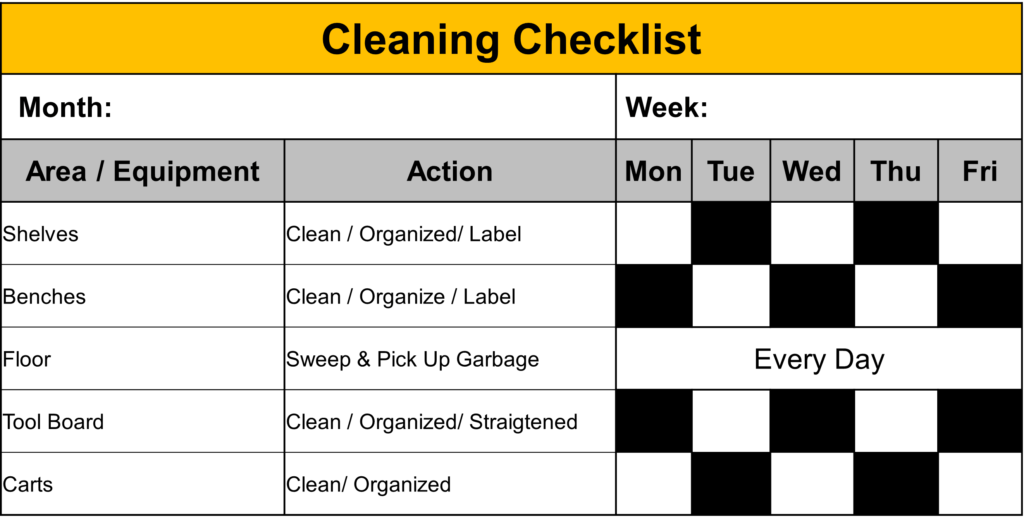
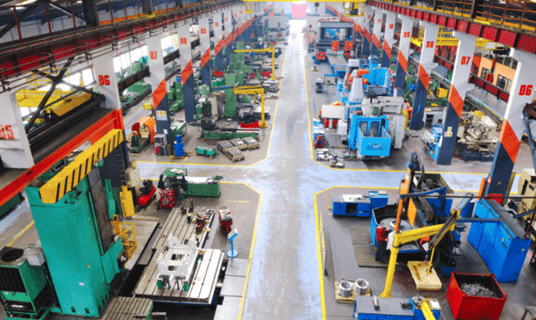
Racks
Each rack will have a location address that anyone can see to find parts to put away or use for an assembly. The racks will also have parts labels with part information on the label so the team can find them quicker
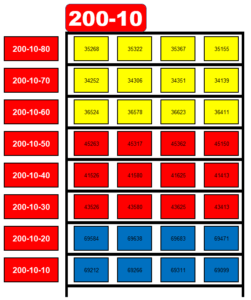
Step 3 - Cleaning Tools In The Work Area
Depending on the environment you are cleaning, you will need to decide what tools are required to be stored in each work area for the end-of-shift cleaning. The most standard items are mops, brooms, dust pans, spray bottles, and rags.
TIP – Make sure you have a disposal plan for all dirty water and rags after your teams have cleaned!
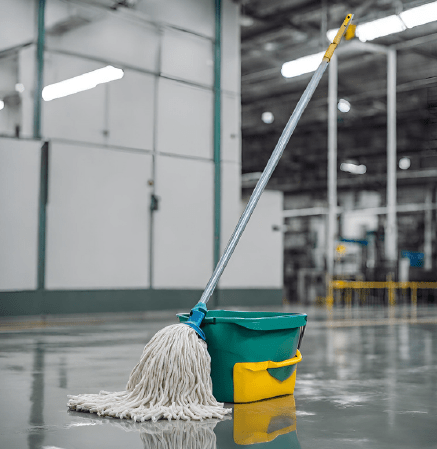
Step 4 - Cleaning Time
Every good 5S implementation will have time allocated to clean the work area. This time designated time is at the same time on each day so everyone creates a habit of cleaning their area. I would recommend that you a lot 5 to 10 minutes at the end of the day for your cleaning time.
The supervisor will be inspecting
the assembly line to ensure that the teams are cleaning properly. They should
also lend a hand in areas where extra effort is needed. Supervisors and
managers play a vital role in demonstrating to the teams that they are willing
to assist and get their hands dirty to make 5S work effectively in their
company.
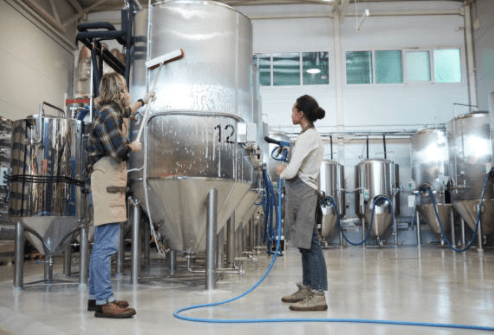
Step 5 - Cleaning Audits
After the workers have left their work area and gone home for the day, you can assess which areas are the cleanest and which areas need more attention to meet the 5S cleanliness standards you have set. Your management team can conduct a surprise audit either while the workers are in their areas or after they have left for the day.
One way to ensure that teams clean their work area properly is to conduct a daily audit of the area. Additionally, implementing a trophy for the team that maintains the cleanest area for the week can be a great morale booster. This trophy can be awarded during Monday morning’s production meeting in front of the entire team, allowing everyone to congratulate the winning team and feel motivated to keep their own areas clean.
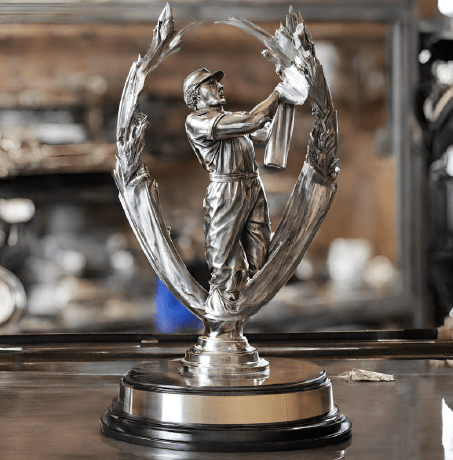
Step 6 - Everyone Cleans
That’s right, everyone should participate in cleaning! As mentioned earlier, supervisors and managers should go to the work areas from time to time and demonstrate that they are willing to assist with cleaning.
I have worked in several factories where managers and supervisors are actively involved in cleaning tasks like painting aisle lines and cleaning under racks during summer shutdowns after a significant line move. Some of the most enjoyable moments I’ve had in a factory have been working with a team to paint lines.