The Eight Wastes In Manufacturing
In everyday manufacturing, many projects get assembled to produce if final item. That goes out the door to a customer. These products are built with many staff that follow the process of how to manufacture these parts. All of these different steps have areas where waste can be found and eliminated within the process.
Many processes can be improved and that is why there are so many professionals looking at lean manufacturing to help eliminate waste and make their business more efficient. The eight ways in manufacturing can be reviewed with your team and should be used as a guideline to help you focus on improving your process.
How The Eight Wastes Were Developed
The Seven Wastes were developed by Taiichi Ohno, Chief Engineer at Toyota. The eighth waste, Skill was added in the 1990’s as more influences were seen in North America. These eight wastes are a major part of Lean Manufacturing and a good guideline for Continuous Improvement.
The Eight Wastes
Each of the waste can affect any business that produces a service or a finished product. In the next sections, we will go over the different wastes and show you the tools on how to eliminate these wastes.
Transportation
Transportation waste is any type of movement of a part or an assembly that does not add any value to the product or service that is being produced. Some ways to eliminate or reduce waste movement are;
- Reduce the number of times a material handler needs to replenish parts in the work area.
- Move items closer to the point of use. If an assembler can walk to Iraq in their area to get apart, rather than another work area, this will make them more efficient.
- Is your warehouse too far? I once worked for a company that moved its warehouse in the middle of the factory to reduce delivery times from the material staff. This move saved the company thousands of dollars and reduced the headcount needed for material handlers.
Inventory
Inventory waste is calculated by the number of parts that are required to support the process. Inventory is sometimes a tricky waste to tackle because too high of an inventory, costs the company money, and too little will create shortages. Ways you can reduce your inventory are;
- Reduce the number of raw materials you are purchasing for your process. Calculate your delivery time and process time to determine the number of parts you will need for your process.
- Calculate the minimum and maximum quantities you need to have in your inventory to make sure you do not run out of these parts. Use the formula below to help you calculate your minimum and maximum quantities.

- Work with suppliers to reduce delivery times and the times to manufacture your parts. Anytime you can save in this process will allow you to reduce the ordering and stocking quantities for your business.
Motion
Motion waste is any unnecessary movement that is performed by a machine or a person. These wastes are evaluated by the team and any non-value-added task should be removed or reduced in your process. Some unwanted motions are excessive walking, reaching, bending, and lifting. Ways you can remove unwanted motion are;
- Moving items closer to the point of use. Moving items closer will reduce travel time for picking parts, reaching for tools, or putting assemblies away. Try to look at your work area layout and see what items can be moved to reduce travel time.
- Reduce travel time to put parts away in the storage racks or warehouse. If your material handler needs to travel to the far end of your factory every time they need to put a part away, it is time to move your process or receiving area.
- Placing all the parts needed in a work area at a good ergonomic height. I always tell teams to place items near the strike zone. For those of you who do not know where the strike zone is, it is above your knees and below your shoulders. Try to keep parts in this area to minimize the motion of bending and reaching.
Waiting
Waiting waste is any time that someone or some machine is idle and not working. If a person is waiting for a sub-assembly to be built and cannot complete their job without this assembly, this is a Waiting waste. The Waiting waste is the same if a machine is waiting for raw material to be delivered so it can be machined. Waiting waste is easy to see and hear, if you see people standing around talking or it’s quiet in your factory, you have waiting waste. To eliminate Waiting waste, you and your team can review the following;
- Process Line Balance – look at your Standard Operation Worksheets to see if all of your work areas are equal in time. Any work areas that are not equal in time, need to be reviewed to see how you can balance the time in the process so no one is waiting.
- Reduce the defects produced in your process – when you have a defect in your process, someone needs to make the repair and usually that person is working in your process. When the repair person is fixing the defect, the line is not moving and the staff is waiting for the next operation.
- Eliminate shortages in your process – Every time you have a shortage in your process, you will have someone waiting for a part to build your product. I know that all processes will come across shortages sometime in their life, just try to reduce the shortages using some of the other lean tools we discussed in the 5S articles.
Overproduction
Overproduction is when a process or work area produces an item before it is required. If your customer demand for your product is 15 per day and you build 20 per day, this is Overproduction. This also applies to production lines, if your main line produces 15 per day and your subassemblies produce 20 per day, the sub-assemblies are making more than what the line requires. Here are some ways to reduce or eliminate overproduction in your process or factory;
- Follow your customer demand and tact time for your process. If you have a few work areas that are working ahead, this means that their area is not balanced with the rest of your process. Review the work done in this area and see how you can balance the time or have the person move to a different work area to help when they are done with the work in their area.
- Balance your process – as stated in the previous step, review your work time balance between all the work areas and make sure they are equal or at least 5% of each other.
Overprocessing
Waste of Overprocessing is when you add additional material or labor into a product that the customer is not paying for. When an employee decides to add an extra layer of paint to your product, this is considered Overprocessing waste. That’s why many automotive companies use robots to apply the optimal amount of paint to car components. Adding extra layers of paint manually would cost thousands of dollars.
Some of the items that you and your team can focus on when you want to eliminate the Overprocessing in your process are;
- Create a clear instruction or quality criteria for your team on how to build your product or service. If the workers in your process are not clear on what is acceptable criteria, they might add more time and effort to achieve a higher standard that is not value added to the product or service. Your standards will help give clarification and eliminate the overprocessing.
- Standardized work techniques from work area to work area. Training each of your staff in your process on how to complete a task the same way will help the staff from adding additional steps in your process. If all staff follow the same techniques and do not alter the process, this ensures that they are following your standard.
- Clear customer requirements – having clear acceptance criteria that have been proved by the customer will help your team follow what the customer wants as a final product. It is a good idea to keep a master sample at the end of your process for your team to refer to in case of questions.
Defects
Defect waste is any defect in a product or service that needs to be repaired or corrected before a customer receives it. Any defect that is found in your process is a waste because you need to place additional manpower to correct the issue. The additional manpower is an extra cost to your company and should always be eliminated. Things you can do to help you reduce defects in any process are;
- Skilled labor – training your staff is a key part of reducing your defects. The higher the skill of the person who works in the area, the lower your defects will be. Create a training plan on how you will keep training your team to make them more skilled. Use a training matrix to keep track of who needs additional training.
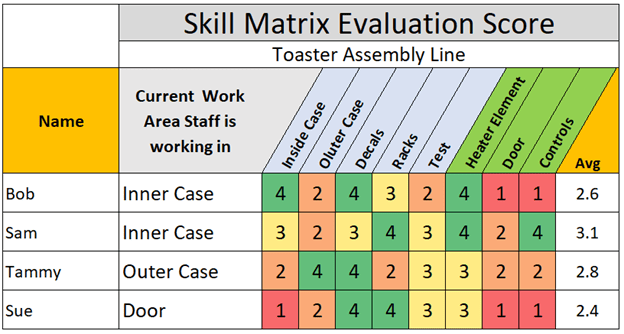
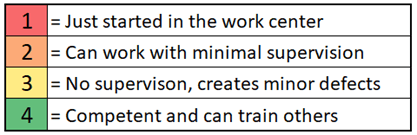
- Focus on repairing the highest occurring defects – with your quality team, determine the defects that occur the most. Find the root cause of the defect and implement this solution to eliminate the defect from occurring in the process ever again. Keep track of all the defects that you correct, each of these our money that you have saved the company.
- Improve your quality process – there are several ways to improve your quality process, but my favorite is to inspect the process and not just at the end of the line. When a business is quality-oriented, everyone focuses on quality not just the quality department. Teaching your staff how to implement in-process checks will help your company reduce defects and improve the quality of your product or service being built.
Skills
The Skill waste was added by Toyota in the 90s when they had issues with recruiting staff. Skill waste is when a company is not utilizing the knowledge that the team members have of the process. When staff have been working in an area for years or months, they will learn skills to improve the work in their work area. If you do not ask and the staff do not tell you the improvements they have made, it is a Skill waste. To reduce the skill waste in your company try these suggestions;
- Suggestion box with a reward – having a suggestion box that your staff can add their ideas to and get rewards, is a good way to encourage teams to think of improvements and boost morale. People who submit suggestions have taken the initiative to help the company save money or improve a process.
- Promotion within the company – promoting staff members who have demonstrated a high level of knowledge and leadership in the process is a valuable way to utilize their skills and improve the overall effectiveness of the business. By doing so, you can not only reward your best performers, but also create a culture of continuous improvement where employees are motivated to learn and grow within the company.
- Small group employee meetings – I have been at a few organizations where Human Resources brings in a group of staff to discuss if there are improvements that they would like to make to the process or the business. Staff that are energetic and open to giving their positive feedback can be utilized in the future for promotions or training to improve their skills. It helps if you bring coffee and Donuts to these meetings, who doesn’t love Donuts?